What is Process Improvement? Definition, Example, and Basics
Imagine your business to be a string. The 2 endpoints of the string are — your people and your product/services. What strings them together are the processes in your business, without which your ends don’t meet.
This thread can either make your business or break it completely. Therefore, to seamlessly continue your business operations, there is often a need for you to revise your processes and bring about improvements.
One of the reasons we hear some of the businesses failing despite their best efforts is as a result of failure in process improvement.
Without further ado, let us get you to familiarise yourself with the concept of Process Improvement.
What is Process Improvement?
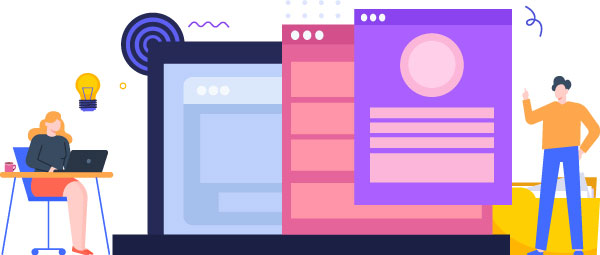
In simpler terms, Process Improvement is nothing but the practice of making the current processes more efficient, faster, and reliable.
It involves identifying and analyzing the current practices and improving them to optimize performance by — finding areas of error, bridging the gap between current processes and ideal standard practices, and improving the overall quality, to ultimately enhance the user experience and customer satisfaction.
These improvements can be in the following fields:
- HR administration
- Sales Processes
- Purchase Processes
- Onboarding
- Contract Processes, etc.
There are different names used for Process Improvement in the industry. Despite having several names, the end goal remains the same — to minimize errors and make room for improvement. Some of the common names of Process Improvement are Business Process Management (BPM), Business Process Re-engineering, and Continual Improvement Process (CIP).
Why is Process Improvement Important?
All businesses are a product of their operations and the practices that actually support it can ultimately help you get rid of inefficiencies in the system.
No matter the process — whether it is the hiring of a new employee, deploying new software, or workflow automating your current processes, there is a process underlying all these activities.
If that process is inefficient in any manner it will produce inefficient and incompetent results and would make your business turn its heads from any profits that it could have generated.
Examples of Process Improvement
Let’s get down to business or rather business process improvement. So, here are a few examples of how you can work on it. There is no defined starting point to it, so the question then arises – where should you be starting? We are going to familiarise you with some of the most necessary changes for improving your processes.
1. Enhancing The Communication & Collaboration Within The Teams
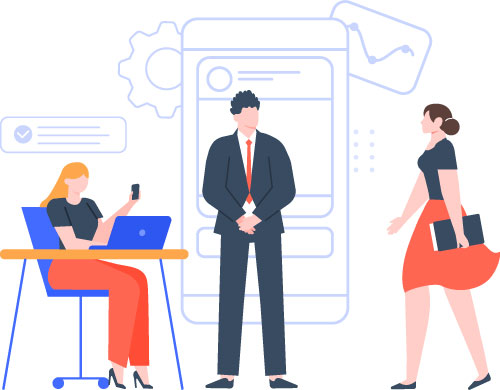
Good communication and collaboration are 2 pillars behind the success of a business. Improvement in this sphere revolves around changing the current dynamics of managing the communication channel.
One of the ways this can be improved is by ensuring that all the team members in the business are aware of their roles and responsibilities, are on the same page, well connected on what the project demands to be done next, and share a common platform for communication and collaboration.
One of the ways this can be facilitated is by the use of certain tools like CRM’s. Also, automating the processes often play a major role as a major part of the process is then taken up by the tools.
Software in place makes sure that there is transparency in the system from day one. It keeps track of all the information in one single place that also ensures a minimum need for contacting colleagues to make updates.
This also cuts down on the number of email exchanges and hence the time taken to dig in to find the relevant emails and information, which can further be utilized.
2. Time and Again Audits in the System
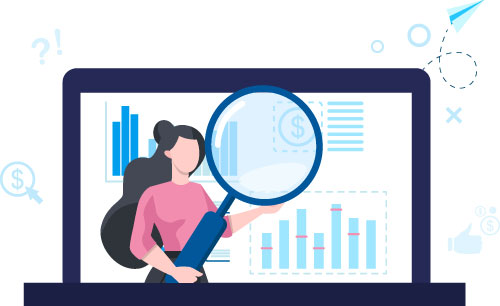
All businesses have goals to achieve and some plans in place but not always are these goals met. Why? Because of inefficiencies in the system. One of the best ways to remove these inefficiencies and bring about continuous improvement in the system is by auditing the process every now and then.
Setting benchmarks that can be measured is how one can go about analyzing everything in the process such as – the time it takes to complete the task, the deliverables, the bottlenecks, deviations, etc. This is often done at a professional research level.
Once there is a set of data in place to examine, you can study it further to set standards for the processes in the future that would be free of the difficulties faced earlier. While the major focus should always be on the effectiveness of process changes, task efficiency should also be a priority to better control production costs.
3. Getting Rid of all the Waste in the Process
One of the most underestimated examples of improving the processes is by the way of eliminating the waste in the business. It is often overlooked how the business processes generate a lot of waste and how that contributes to hindering the overall growth.
We can tell you with an assurance that if you can center your focus on identifying the key areas that produce this waste and eliminate those, it would save you a fortune of time and money and would help you progress better.
One of the ways that can be done is by following the lean project management tactics. It focuses on looking for wastes in the process such as:
Any form of defects in the system, Overproduction, Inventory going to waste, Unnecessary communication in the workplace, under-utilized talent, to name a few.
If you can spot these and go about restructuring with corrective measures in the future, you would see yourself moving in the direction of an efficient model.
Best Practices for Process Improvement
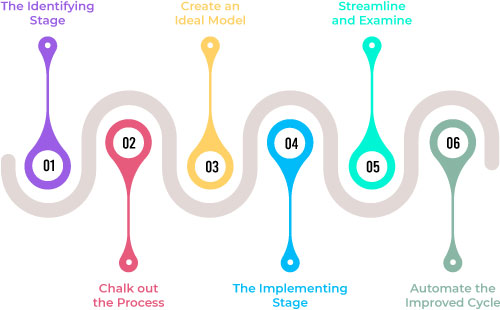
Now that you’re aware of the examples of Business Improvement, this section is what you need to know in order to be implementing those examples. Here are a few best practices you need to take up to implement an improved model:
- The Identifying Stage: Check your current status and see what needs to improve. Look out for processes that need improvisation.
- Chalk out the Process: Look for minute details – the team members involved, the process stages, the goals to be met, the correlation between all the elements, etc.
- Create an Ideal Model: Work on creating a model that addresses the major problems such as the waste in the system, the unnecessary costs involved, process deliverable delays, etc.
- The Implementation Stage: Implement the process in the form of improvements with opportunities like automation, rearranging workflow, documentation, required training, etc. It depends on the nature of the improvement in your business process.
- Streamline and Examine: Once executed, it’s time for measuring – what worked and what did not. Identify areas that can be improved and work on them.
- Automate the Improved Cycle: Once you can make out what works and what does not, it is time for a faster flow of the improved process with an automated improved workflow.
Wrap Up
Once you implement these examples in your day to day business operations, you are bound to see a difference but you need to remember one thing – it is not a one time process that is going to fetch you results over a long period of time but rather a continuous practice you need to take up to see changes. These examples should be practiced as an ongoing activity.
Having said that, you are trained enough to be improving your own business process cycles and you should get onto it right away!